ATEX AND EX ENVIRONMENTS
Safety for potentially explosive atmospheres with PRE-ELEC® electrically conductive plastics
Imagine an environment where the air contains a potentially explosive substance, such as oil or chemical fumes, sawdust, or baking flour. Then, some innocent equipment or an ungrounded person creates a spark of electricity that ignites the substance flowing in the air. People can get hurt in the explosion, and the buildings can suffer damage or even burn down.
This kind of explosion could happen at a gas station, a coal mine, or a wheat mill. A better-known example is the danger of smoking at a gas station. But many people don't realize that baking flour, for example, can be explosive. Or that electric discharge from an electrically resistant material can ignite an explosion.
Explosive environments
In explosive (Ex) environments, electric sparks are especially dangerous. Explosions can occur when these factors combine:
- Dry air
- Explosive substances in the air, such as
- Oil fumes, gasses
- Dust from agricultural products, such as flour, sugar, cereals, soybeans, rice, etc.
- Dust from coal, medicines, wood, textiles, etc.
- Ignition source (e.g., ESD)
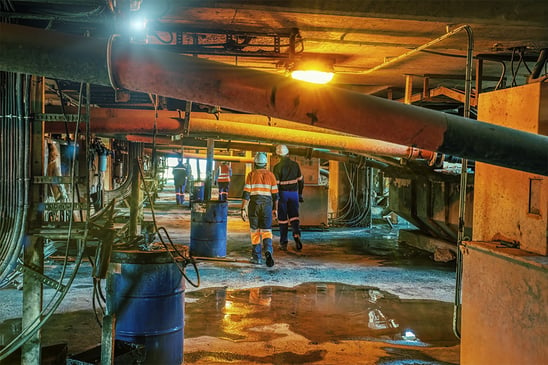
Mines are often explosive environments.
ATEX directive and electrically conductive plastics
The European Union's ATEX Directive (2014/34/EU) covers equipment and protective systems intended for use in potentially explosive atmospheres. For raw materials, there's no specific directive, but the materials need to be compatible with the requirements for the whole equipment.
Plastics are increasingly being used in ATEX environments to replace heavy, corrosive, and rigid materials, such as metals. However, due to their insulative properties, plastics can cause uncontrolled static discharge, leading to explosions and human casualties. Electrically conductive plastics are an excellent solution for ATEX areas when their surface resistance is <109 ohms.
Need more information? Contact our ATEX expert:
Examples of ATEX environments:
Designing ATEX-compatible equipment together with Premix
Premix's electrically conductive PRE-ELEC® plastics typically have much lower surface resistance than 109 ohms, and they can be customized to fulfill the customer's specifications. Compared to metals, plastics are cheaper, lighter, and corrosion-resistant. In addition, injection molding enables freedom in form design. Flame retardancy can be added as an additional property.
Premix already has a wide variety of electrically conductive plastics, and we often develop suitable materials for our customers. From our Data Center, you can find a list of readily offered raw materials with parameters like surface resistance and temperature stability.
Raw materials for ATEX equipment can’t be certified as the whole item must be certified and withstand all the standards according to the ATEX utilization area classification.
INDUSTRY SOLUTION
Packaging industryMATERIAL SOLUTIONS
Sheets Boxes and pallets Films and filaments Flexible tubes, hoses, and profiles DATA CENTERFrequently asked questions (FAQ)
We have collected here some questions on ATEX from our customers, external experts, and Premix colleagues.
Contact us if you have any further questions!
When do I need Ex-compatible material?
The Ex-Equipments used in explosive atmospheres are regulated by European Union Directive 2014/34/EU, the so-called “ATEX Directive.” The producer of Ex Equipment or Ex Components must make sure that the material requirements are fulfilled.
The next question you probably have is now: How do I know if ATEX Directive applies to my equipment?
A good description of Ex-equipment can be found in the ATEX 2014/34/EU Guidelines - 2nd Edition December 2017 – document: “ equipment means machines, apparatus, fixed or mobile devices, control components and instrumentation thereof and detection of prevention systems which, separately or jointly, are intended for the generation, transfer, storage, measurement, control and conversion of energy and/or the processing of material and which are capable of causing an explosion through their own potential sources of ignition;” On the other hand, the manually (by hand) operated devices, for example, hand-operated valves are considered as “simple products” and excluded from the scope of ATEX Directive.
One has to remember, though, that even if the product is considered a *simple product* and therefore excluded from the ATEX Directive, the producer should always make sure that if the product is used in Ex environments, the materials used in the product construction will not cause any safety hazards. One example relates to the use of insulating plastic materials on excessively large surfaces. This will cause the risk of static electricity. Fortunately, these kinds of risks are easy to avoid by using electrically conductive plastic materials.
More information and concrete examples can be found in the pdf-document: “ATEX 2014/34/EU Guidelines – 2nd Edition December 2017” which can be downloaded from the European Union website: “Equipment for potentially explosive atmospheres (ATEX).” From the document, you’ll find examples of the equipment excluded and not covered by ATEX Directive and also a “Borderline list,” which provides more examples of products within or outside the scope of the ATEX Directive.
In case you are not certain whether the ATEX Directive applies in your own case, you can always turn to the National Authorities who are responsible for implementing the ATEX Directive (in Finland, Finnish Safety and Chemicals Agency / Tukes).
In which areas are ATEX materials needed?
The materials used in Ex Equipments and Ex Components in all kinds of Ex Environments (i.e., Ex-Zones) have to comply with the requirements set in ATEX Directive. In some cases, the normal, insulating plastic materials are used in the equipment parts which are not generating static electricity during the use of the compactly installed equipment. In those cases, plastic parts should be labeled with special warnings stating that cleaning and wiping the equipment with dry cloths is forbidden.
ATEX Directive sets the requirements only for equipment and components. The other hazards associated with static electricity in industrial processes and environments are considered in IEC/TS 60079-32-1 Technical Specification: Explosive atmospheres - Part 32-1: Electrostatic hazards, guidance. These processes include the handling of solids, liquids, powders, gases, sprays, and explosives.
What are the conductivity requirements for Ex-compliant materials?
The material requirements for plastics materials used in Ex environments have been described in harmonized IEC EN 60079-0 Standard “Explosive atmospheres – Part 0: Equipment – General requirements”. In chapter 7, you’ll find the requirements for “non-metallic enclosures” and “non-metallic parts of enclosures.”
The requirements related to avoidance of electrostatic charges of non-metallic materials are listed in chapter 7.4, “Electrostatic charges on external non-metallic materials.” The standard states that “Equipment is intended to be designed so that under normal conditions of use, the danger of ignition due to electrostatic charges on external surfaces or enclosures is avoided.” The standard lists several different techniques to control the build-up of static electricity. The first of the techniques is to choose materials so that their surface resistance levels must stay below 1 GΩ at (50 ± 5) % relative humidity or below 100 GΩ at (30 ± 5) % relative humidity.
In most cases, the parallel use of these techniques is recommended. From a material selection perspective, the easiest way to comply with the requirements is to make sure that all the non-metallic materials are made out of electrically conductive or static dissipative materials.
Is there a need to ground electrically conductive plastics in Ex Environments?
Yes. It is very important to ground the dissipative and conductive materials in order to take out the generated charges in a controlled manner. It is also stated in IEC EN 60079-0 standard that non-grounded, conductive, and dissipative materials can cause higher ESD risk than isolated materials.
In explosive atmospheres, all metal and other conductive or dissipative materials must be connected to earth with the exception of very small items. Isolated conductive or dissipative material can cause higher ESD risk than insulators. For dissipative materials with a surface resistivity exceeding 10 GΩ, earthing may not be necessary. Detailed information can be found in IEC's Technical Specification IEC/TS EN 60079-32-1:2013. The technical specification provides recommendations for the control of static electricity in equipment, product, and process levels. E.g., earthing of conductors, reduction of charging, and restriction of chargeable areas of insulators.
What other requirements for Ex-compatible materials are there, apart from conductivity?
The other material requirements are temperature resistance and UV resistance. The requirement ranges are set by the original equipment manufacturer at the product design phase, and they depend on the equipment's operating conditions and exposure to the weather conditions. Paragraphs 26.8 and 26.9 in IEC EN 60079-0:2017 standard describe how the thermal endurance to heat and cold should be determined.
The temperature requirements vary between plastics and elastomeric materials (rubbers and thermoplastic elastomers). For plastics, one has to provide the information on TI, i.e., the material’s temperature index, whereas, for elastomers, the COT (i.e. continuous operation temperature) will be enough. The UV resistance will be required for both materials in case the product is exposed to UV light. In that case, the carbon black filled electrically conductive materials are the best choice due to carbon black's excellent UV-protection properties.
What is the TI index?
TI index, i.e., temperature index, has been determined on IEC EN 60079-0 standard’s part Plastic materials 7.1.2.2 d):
“the temperature index TI, corresponding to the 20 000 h point on the thermal endurance graph without loss of flexural strength exceeding 50 %, determined in accordance with IEC 60216-1 and IEC 60216-2 and based on the flexing property in accordance with the ISO 178. If the material does not break in this test before exposure to the heat, the index shall be based on the tensile strength in accordance with ISO 527-2 with test bars of Type 1A or 1B.
As an alternative to the TI, the relative thermal index (either RTI – mechanical strength or RTI – mechanical impact) may be determined in accordance with ANSI/UL 746B.
From where can I get the approval for my Ex Equipment?
The testing and certification are carried out by a “third-party” certification body (“Notified Body”). The list of certified Notified Body companies can be found at http://ec.europa.eu/growth/tools-databases/nando/index.cfm?fuseaction=directive.notifiedbody&dir_id=153101. The certified equipment will be marked with the ‘Ex’ symbol.
In what cases is the UL-flame retardancy listing required in the ATEX area?
The ATEX Directive does not include a requirement for flame retardancy properties. As for the temperature resistance, the chosen materials should not burn or be self-extinguishing.
In standard IEC 60079-0, the ANSI/UL, norms are mentioned only with UV-resistance requirements of non-metallic materials. UV requirements meeting ANSI/UL 746C are considered satisfactory.
Can Premix ensure that the final product is Ex approved?
In short: No.
In a material supplier role, Premix provides a raw material with certain material parameters, like surface resistance and temperature stability. The raw material selection will be carried out based on the information provided by raw material and component suppliers. All materials and components have to pass the product's Ex-certification process, which depends on the equipment, chosen Ex-shielding methods, and equipment’s operating temperatures. Based on this information, Premix is able to recommend the most suitable material, but the final and official material approval will be received only from the Ex-certification testing.