Electrically conductive plastics
PRE-ELEC® — a global leader in conductive compounds
Controlling static electricity
It is possible to add electrical conductivity to plastics with several additives, but carbon black has established its position as the most widely used electrically conductive additive.
Carbon black offers a superior price-performance ratio and stable properties over time. Typically, carbon black is most suitable for compounds with surface resistance of up to 106 Ω. Carbon black can also be used on dissipative area of up to 108 Ω in certain applications.
We introduced our first electrically conductive plastic compound in 1983 as one of the first companies in the world. Today, the PRE-ELEC® product family covers wide areas of the conductivity spectrum and a large selection of base polymers.
Let Mr. Premix and Mr. Statix explain to you how electrically conductive plastics can protect from electric shocks!
Adding carbon black improves conductivity
Carbon black is a highly conductive material with low density compared to metals. By mixing it into plastic, it is possible to gradually alter the plastic's electrical properties to decrease its resistivity. The resistivity of the compound correlates with the average distance between carbon black particles within the plastic matrix.
At a certain loading level called percolation threshold, the carbon black particles are close enough to form an electrical contact, which can be seen as a significant change in the conductivity. Further, carbon black addition increases the conductivity significantly at first and gradually forms a plateau, which is dependent on the conductivity level of the used additive.
Figure 1. Percolation curve. Adding carbon black decreases resistivity.
Figure 2. Resistance spectrum and PRE-ELEC® compounds and concentrates.
More information on how the magic works in our blog post: Carbon black magic turning electrically conductive plastics into products
Drivers for using electrically conductive plastics
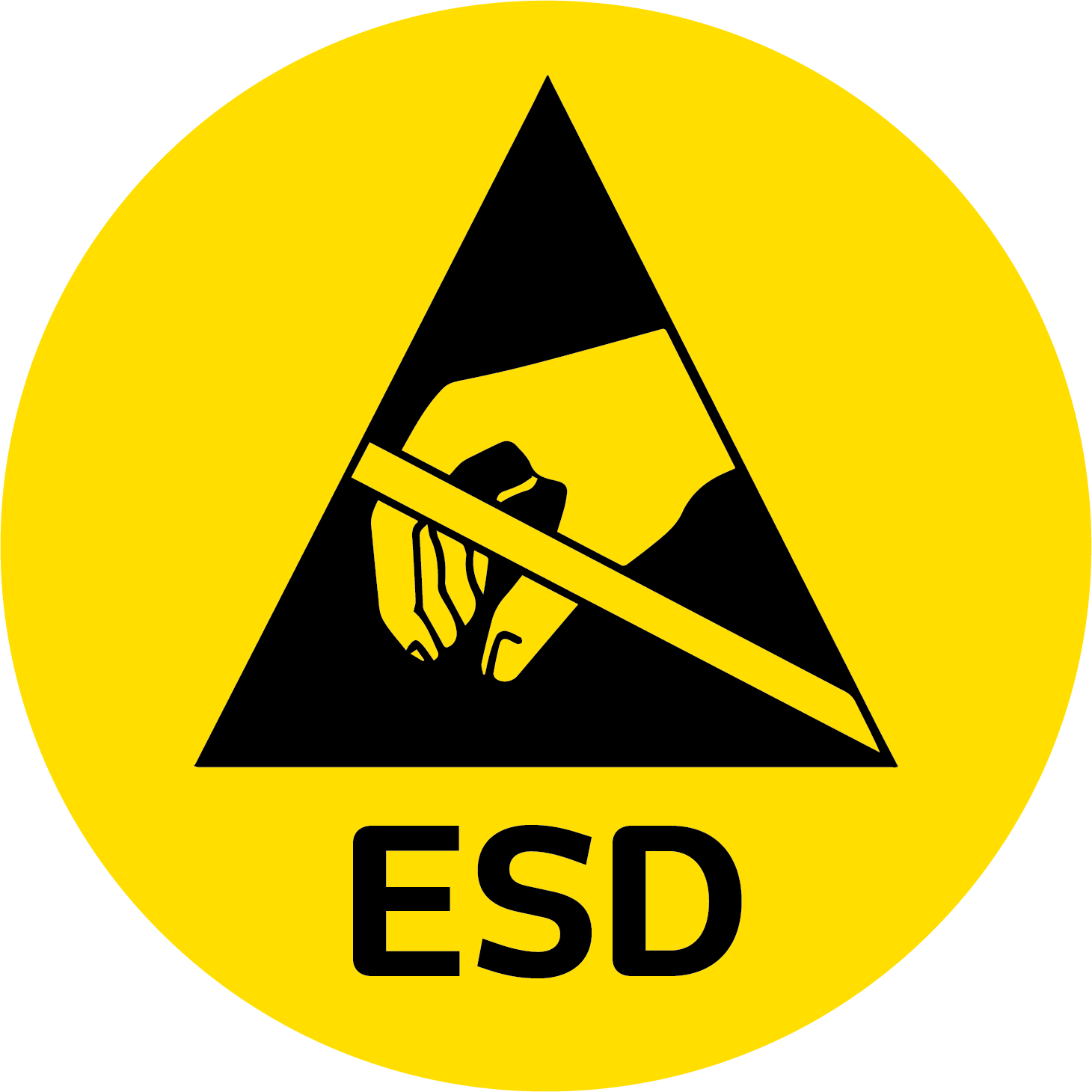
Protecting against unintentional electrostatic discharges (ESD)
Protecting components from static electricity during electronics production, transportation, and handling.
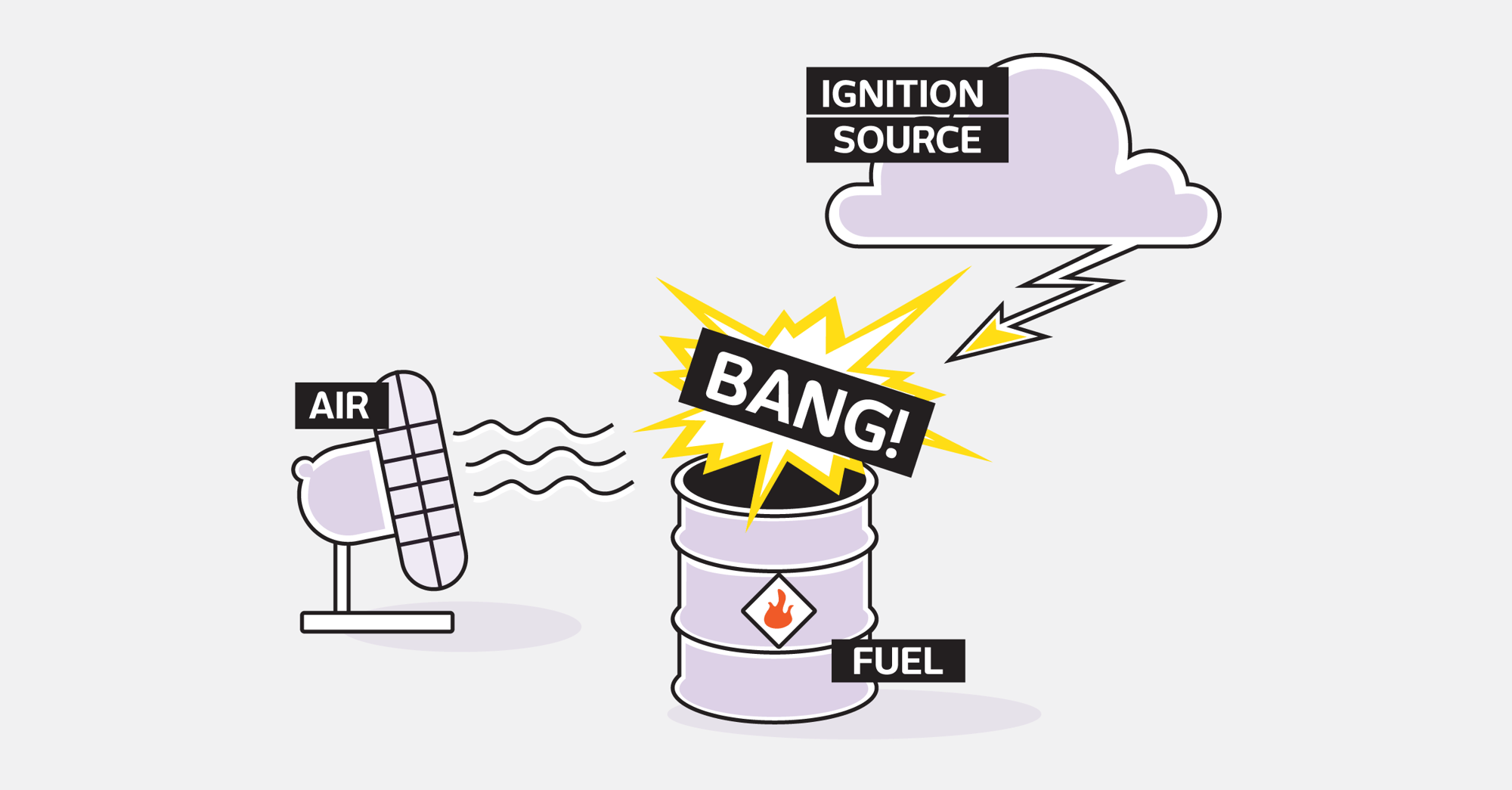
Protecting against accidents in explosive (Ex) environments
Eliminating the static discharges which can cause explosion and fire risks in, for example, the automotive, mining, and process industries.
In addition, plastics' light weight, mass-production capabilities, economicality, and freedom of design bring a lot of value when selecting the source materials.
PRE-ELEC® is available as
Base polymers
PE, PP, PS, ABS, PC, PC/ABS,
ABS, PA6, PBT, TPU, TPE
Processing types
Extrusion
Injection molding
Blow molding
Film blowing
Post-processing
Foaming
Thermoforming
Base polymers
PE-HD, PE-LLD, EVA, PP,
PS, PA6
Processing types
Extrusion
Injection molding
Blow molding
Film blowing
Post-processing
Foaming
Thermoforming
Other information
Typical concentrate usage ranges from 40 wt-% to 60 wt-% depending on the surface resistance target. Higher dosages are also possible if the process tolerates higher process viscosities.
In addition, plastics' light weight, mass-production capabilities, economicality, and freedom of design bring a lot of value when selecting the source materials.
Boost your business with electrically conductive plastics concentrates
Carbon black concentrates are an excellent way to reduce raw material costs. In PRE-ELEC® concentrates, the carbon black content has been optimized to the highest possible level. When striving for maximum cost efficiency, recycled plastics or regrind from your own process can be used to dilute the concentrate. One small yet innovative step can lead to significant cost savings.
Besides the economic advantages, concentrates also allow the modification of product properties. To impart stiffness and strength to the finished product, the reinforced plastic can be used for dilution.
MORE INFORMATION
Benefits of concentratesTackling processing challenges
Premix has over 30 years of experience in producing high-quality functional plastics. Our electrically conductive plastics have very good dispersion (even distribution of carbon black in plastic). Overcoming the following challenges is part of our expertise:
Processing instructions
This material further exaplains extrusion and injection molding carbon black filled electrically conductive compounds and concentrates.
Processing PRE-ELEC®Shear sensitivity
High shear forces often lead to breakage in the carbon black network. This results in higher resistance of the molded parts. Surface resistance is always a sum of material and molding details such as mold cooling, melt temperature, and parts' wall thickness and shape.
Moisture sensitivity
All carbon blacks are moisture sensitive; some more, some less. Moisture is one of the most typical problems faced by converters. This can have an effect on how easy it is to process into an end product.
Premix always offers an opportunity to dry the compound before delivery and drying recommendations for each material.
Impact on mechanical properties
Adding carbon black to plastic will change the mechanical properties, e.g. impact strength and tensile strength. Our expertise lies in the optimization and balancing of various material properties on a good level for the products' intended use application.
Impact on processing viscosity
Carbon black filling can increase the melt viscosity of a plastic. The effect depends on multiple factors including filler loading, surface chemistry, and specific surface area of the used carbon black.
Our expertise is to retain the viscosity and other necessary properties on a suitable level while introducing electrical conductivity.
Keeping your production lines clean
Carbon black can create a mess on a production line. By letting us mix the carbon into plastics, you can keep your production lines clean.